1. Filament
In the manufacturing process of synthetic fibers, after the spinning fluid (melt or solution) is subjected to spinning forming and post-processing, the resulting fibers with a length in kilometers are called filaments. Filaments include monofilaments, multifilaments, and cords.
(1) Monofilament
Originally refers to a continuous single fiber spun with a single-hole spinneret, but in practical applications, it often also includes a few-hole yarn composed of 3-6 single fibers spun from a 3-6 hole spinneret. Thicker synthetic fiber monofilaments (0.08-2mm in diameter) are called bristles, which are used to make ropes, brushes, daily net bags, fishing nets or industrial filter cloths; thinner polyamide monofilaments are used to make Transparent women's socks or other premium knitwear.
(2) Multifilament
A thread consisting of dozens of individual fibers. Multifilaments of chemical fibers generally consist of 8 to 100 single fibers. The vast majority of clothing fabrics are woven with multifilaments, because multifilaments composed of multiple single fibers are more flexible than monofilaments of the same diameter.
(3) Cord wire
The thread used to manufacture tire cord is composed of more than one hundred to several hundred single fibers, commonly known as cord thread.
2. Short fiber
The products of chemical fiber are cut into lengths of several centimeters to ten centimeters, and the fibers of this length are called short fibers. According to the different cutting length, the staple fibers can be divided into cotton staple fibers, wool staple fibers, and medium and long staple fibers.
(1) Cotton staple fiber
The length is 25~38mm, the fiber is relatively thin (linear density is 1.3~1.7dtex), similar to cotton fiber, mainly used for blending with cotton fiber, such as blending cotton polyester staple fiber with cotton fiber, the obtained fabric Called "polyester-cotton" fabric.
(2) Hair type short fibers
The length is 70-150mm, the fiber is thicker (linear density 3.3-7.7dtex), similar to wool, mainly used for blending with wool, such as wool-type polyester staple fiber and wool blending, the resulting fabric is called "wool polyester" "Fabric.
(3) Medium and long fibers
The length is 51-76mm, the thickness of the fiber is between the cotton type and the wool type (linear density is 2.2-3.3dtex), and it is mainly used for weaving medium and long fiber fabrics.
In addition to being blended with natural fibers, short fibers can also be blended with short fibers of other chemical fibers, and the resulting blended fabrics have good comprehensive properties. In addition, short fibers can also be spun purely. In the current production of chemical fibers in the world, the output of short fibers is higher than that of filaments. According to fiber characteristics, some varieties (such as nylon) mainly produce filament; some varieties (such as acrylic) mainly produce short fibers; and some varieties (such as polyester) have a relatively close ratio of the two.
3. Thick detail wire
Thick and thin silk is referred to as T&T silk for short. From its shape, you can see the alternate thick knots and details, and after the silk strips are dyed, you can see the alternating dark and light color changes. Coarse and fine filaments are produced by uneven drawing technology after spinning and forming. The difference in the properties of the two parts of filaments can be controlled in production, and their distribution is irregular and in a natural state.
Thick and thin filaments have low strength, large elongation at break, strong heat shrinkage, good dyeability, and easy alkali weight reduction processing. These characteristics can be fully utilized to develop unique textiles. The physical properties of the thick and thin filaments are related to factors such as the diameter ratio of the thick and thin threads. General coarse and fine filaments have higher elongation at break and shrinkage in boiling water and lower breaking strength and yield. Its strong shrinkage properties can make thick and fine yarns mixed with other yarns to form different shrinkage mixed filaments. In addition, the thick and thin sections of thick and thin filaments are easy to deform and have low strength, which should be paid attention to in the process of weaving, dyeing and finishing. The original thick and thin yarns were round yarns. With the development of thick and thin yarn production technology, some special thick and thin yarns appeared one after another, such as special-shaped thick and thin yarns, mixed thick and thin yarns, microporous thick and thin yarns, and fine denier thick and thin yarns. Detail silk, etc., they have a special feel and style, or have a special suction, and are mostly used to develop high-end fabrics.
4. Deformed yarn
Textured yarns include all textured filaments and yarns, such as stretch yarns and bulked yarns.
(1) Elastic yarn
That is, the deformed filament can be divided into two types: high elastic wire and low elastic wire. Elastic yarn has good stretchability and bulkiness, and its fabric is close to wool, silk or cotton in terms of thickness, weight, opacity, coverage and appearance characteristics. Polyester elastic yarns are mostly used for clothing, nylon elastic yarns are suitable for the production of socks, and polypropylene elastic yarns are mostly used for household fabrics and carpets. The deformation methods mainly include false twisting method, air jetting method, hot air jetting method, stuffing box method and forming method.
(2) Bulk yarn
That is, using the thermoplasticity of polymer compounds, two kinds of synthetic fiber tops with different shrinkage properties are mixed in proportion. After heat treatment, the high-shrinkage tops force the low-shrinkage tops to curl, so that the mixed tops have stretchability and fluffy. Textured yarn for wool. At present, the output of acrylic bulky yarn is large, which is used to make knitted outerwear, underwear, wool, blanket, etc.
5. Differential fiber
Differential fiber is a loanword from Japan. It generally refers to the fiber material obtained by physical deformation or chemical modification on the basis of the original chemical fiber. It is obviously different from ordinary chemical fiber in appearance or internal quality. Differential fibers not only improve and improve the performance and style of chemical fibers but also endow chemical fibers with new functions and properties, such as high water absorption, electrical conductivity, high shrinkage, and dyeing properties. Since differentiated fibers are mainly used to improve the simulation effect, comfort and protection, they are mainly used to develop clothing textiles such as wool-like, hemp-like, and silk-like, and some of them are used to develop decorative textiles and technical textiles.
6. Special-shaped fiber
In the spinning and forming process of synthetic fibers, fibers or hollow fibers with non-circular cross-sections spun by special-shaped spinneret holes are called special-shaped cross-section fibers, or special-shaped fibers for short. At present, there are dozens of types of special-shaped fibers. About 50% of polyester fibers, polyamide fibers and polyacrylonitrile fibers sold on the market are special-shaped fibers.
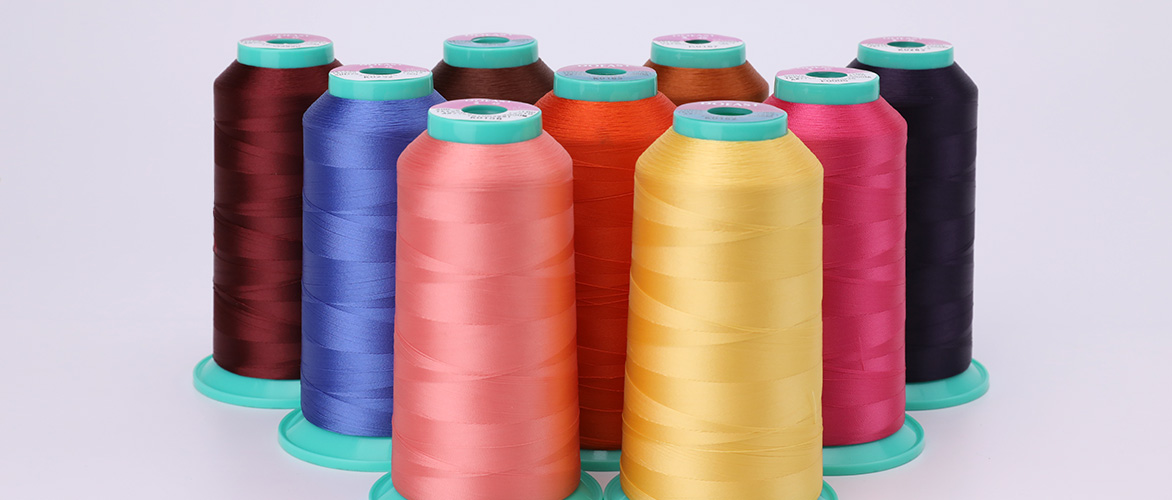
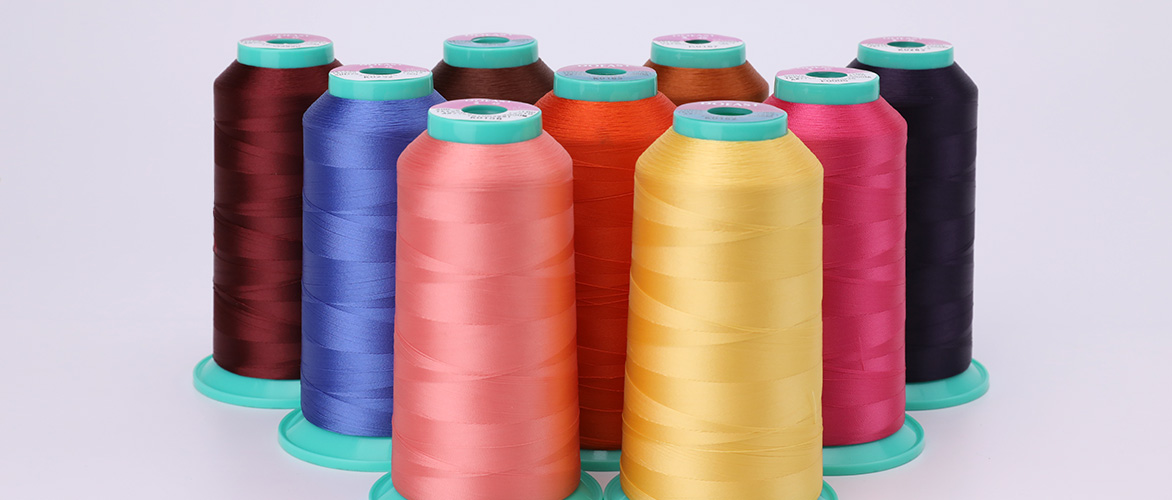